Controlling material temperatures in web processes can be challenging, but it’s also a must. A product’s temperature often impacts its behavior in processing, which can have consequences in everything from adhesion and curing to dimensional stability and product quality.
Heat transfer rolls (HTRs) are indispensable in managing these temperatures, ensuring web materials maintain the desired thermal conditions for optimal performance.
From cooling films in food packaging to heating substrates in laminating processes, precision engineered HTRs play a critical role in virtually endless manufacturing application scenarios. In this article, we take a close look at the science behind HTRs to explore their functionality, design considerations, material selection, and practical applications.
We’ll also review the process PRS takes to help customers make optimal material and design decisions and achieve their thermal management goals.
Heat Transfer Rolls: Core Functionality in Web-Based Production Processes
In the simplest terms, HTRs are designed to either add or remove heat from a web material as it moves through a manufacturing process. The fundamental principle behind HTRs’ operation is the efficient transfer of thermal energy, which is crucial for processes requiring precise temperature control. Thermal transfer is achieved through a fluid medium — typically water, often with appropriate additives — which flows within the roll, absorbing or releasing heat as needed.
Heat transfer rolls can be referred to based on their function within the process:
Chill rolls are used to cool down the web material, often immediately after a heating or drying process, or as part of a cooling cycle to stabilize the material.
Heating rolls are typically used to warm a web material, ensuring proper adhesion, curing, or other temperature-dependent processes (such as embossing thermally sensitive materials).
HTR Design Considerations for Optimal Performance
In designing heat transfer rolls, engineers take into account several critical factors that can influence efficiency and effectiveness. Understanding these considerations is essential for optimizing roll performance and ensuring consistent product quality.
1. Fluid Dynamics and Turbulence
Fluid dynamics play a key role in HTR performance. Turbulent flow within the roll is desirable, as it enhances heat transfer by creating a higher rate of energy exchange between the fluid and the roll surface. Engineers often use computational fluid dynamics (CFD) models to design the internal channels of the roll, selecting flow patterns to maximize turbulence while minimizing pressure drop.
2. Pressure Drop
While turbulence is essential, it must be carefully balanced with pressure drop. Excessive pressure drop can lead to inefficient fluid flow, reducing the roll’s heat transfer capability. The ultimate goal is to design a roll that achieves turbulent flow without a significant pressure drop, thus maintaining efficient thermal management.
3. Wrap Angle and Dwell Time
Wrap angle refers to the extent to which the web contacts the roll, while dwell time describes the duration of contact between the material and the HTR. Dwell time is influenced by roll diameter, wrap angle and web speed. Roll surface characteristics, such as surface finish and texture, can also affect heat transfer.
A larger wrap angle and longer dwell time increase the contact area and duration, which will enhance thermal exchange between the roll and the web material. Engineers carefully optimize these factors based on the specific requirements of the application.
Material Selection for Heat Transfer Rolls
The material selected for HTRs can have a direct impact on their durability, efficiency, and suitability for specific applications. Common materials used include:
- Carbon steel – Known for its strength and durability, carbon steel is often used for its high thermal conductivity and resistance to wear
- Aluminum – Lighter than steel, aluminum offers excellent thermal conductivity, making it an option for applications where weight is a concern
- Stainless steel – Resistant to corrosion and capable of withstanding high temperatures, stainless steel is suitable for applications in the food and pharmaceutical industries where hygiene is paramount
Each material has its advantages and trade-offs, and the choice depends on the requirements of the specific process — such as thermal conductivity, weight, corrosion resistance, availability, and cost.
Dispelling Common Misconceptions About HTRs
Basic roller technology has long been used in industries like paper manufacturing, printing, and textiles since the early 20th century, primarily for guiding and handling web materials. By the 1950s and 60s, as industrial processes became more sophisticated and materials became more diverse and complex, more advanced rolls were developed to handle thermal transfer needs.
Since then, advances in precision manufacturing, along with improved understanding of fluid dynamics, allowed for the creation of rolls that can better transfer heat and maintain consistent temperatures. Computational fluid dynamics and computer-aided design have further evolved HTRs, along with more advanced materials and more widespread use of web processes in manufacturing.
Even so, persistent myths about heat transfer rolls can lead to incorrect specifications and suboptimal use. These are a few of the most common misconceptions that can create obstacles to achieving optimal heat transfer and roll performance.
Myth #1: All HTRs are the same.
Heat transfer rolls are designed using a wide variety of materials, internal structures, and engineering to suit specific applications. Proper design and customization are essential for maximizing performance.
Myth #2: Rotational direction has to match flow direction.
In reality, for most heat transfer rolls, the direction of rotation does not impact the fluid flow within the roll. This misconception can lead to unnecessary complications in roll operation.
Myth #3: Roller temperature can be controlled solely by flow rate.
Fluid flow rate is crucial, but it’s not the only factor to consider. Achieving the desired temperature involves a balance between flow rate and the temperature difference (ΔT) across the roll. Proper design ensures both parameters are optimized for consistent performance.
Working with the PRS Roll Experts: What You Need to Know
Collaborating effectively with PRS expert engineers and roll crafting artisans is key to ensuring you get the best heat transfer roll for your needs. As with any precision design project, detailed specifications and information sharing have a direct impact on the process and outcome. Here’s what to anticipate and how to prepare for your conversations with a PRS roll expert.
1. Provide details on the process in which your HTR is needed, including:- Operating temperatures
- Web material specifications, including thickness, composition, and any special properties
- Typical line speeds and tensions used in your production line
- Environmental conditions, such as humidity, dust, or chemical exposure
- Heating or cooling needs
- Desired temperature range
- Surface finish requirements, such as roughness average (Ra) values or coatings
- Customization options for your specific application
- Material recommendations based on your process needs
- Advice on the maintenance and expected lifespan of the roll
Depending on your specific needs, it may be helpful to discuss similar projects PRS has handled, to better understand our capabilities and experience, and to proceed with confidence on your HTR project.
How to Ensure Optimal Performance of Your Heat Transfer Rolls
Heat transfer rolls are critical components in modern converting processes, providing the kind of precise thermal management that’s now essential for high-quality manufacturing on modern web processing lines.
When you understand the complexity and nuanced interplay between design, material selection, and application, your partnership with the roll experts at PRS can become a powerful asset. You’ll be better equipped to make informed decisions that enhance the efficiency and quality of your processes, ensuring your HTRs are optimized for your specific needs and applications.
Close collaboration with the roll experts at PRS can help you achieve maximum roll performance and lifespan. Even more important, your PRS partnership can help you drive innovation and continuous improvement in your manufacturing operations. For more information on how PRS can help you precision-engineer, design, and craft the heat transfer rolls your process depends on, contact our roll experts today. We’re always ready to provide customized solutions tailored to your specific requirements — just click below to get started.
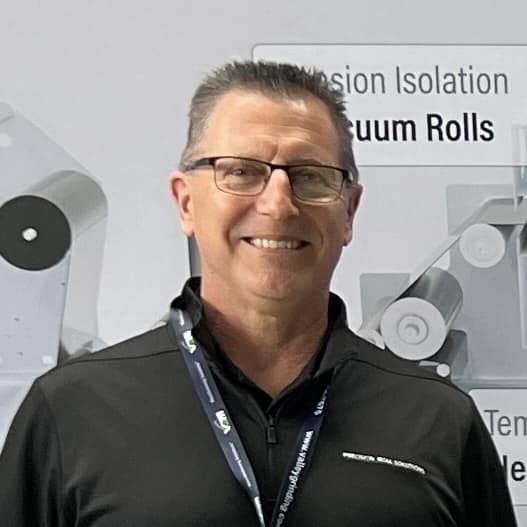
Written by Pete Eggen
Product Manager for Rolls, MECA Division For decades, Pete has specialized in roller design and application engineering, with a focus on the printing, coating, and web converting industries. His extensive engineering expertise encompasses web handling applications product specialties that include heat transfer rolls, custom processing rolls, and vacuum rolls. His wealth of experience has enhanced process and product performance for leading manufacturers worldwide. For over six years at PRS, Pete’s key responsibilities include design and application engineering, project management, and sales. Pete works closely with PRS customers to identify problems and generate solutions through creative engineering applications. He guides customers through the sales process to estimate, quote, and clarify terms and conditions, and he manages customer projects through production and post-sale service. Pete finds the diverse group of customers and the endless variety of applications and innovative products among the most compelling aspects of his role at PRS.
Share Article:
Subscribe to PRS Blog Digest
Share Article:
Connect with
PRS Experts
Questions? Tough challenge? Switching vendors? The PRS experts are here to guide you to your next-level web converting roll solution. Set up a consultation today!