Heat Transfer Rolls
VIEW SPECIFICATIONS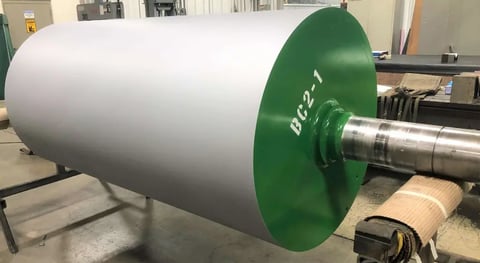
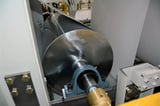
.webp?width=160&height=120&name=DSC_8166%20(2).webp)
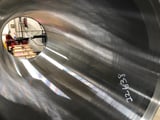
Heating and cooling web substrates is an ever-present process in web converting applications. This explains why the quality and performance of heat transfer rolls are so important — and likely why heat transfer rolls are known by many names, including: chill rolls, chill cans, cooling rolls, chiller rolls, heat rolls, hot rolls, hot cans, and hot oil rolls.
Regardless of the term used, heat transfer rolls have one primary purpose — to transfer heat energy. The direction of the transfer dictates the action. Transferring energy into the process causes heating. Transferring energy out causes cooling.
- Single wall design: The simplest form of roller, being a sealed hollow pipe with hot or cold fluid running through it. This cost-effective design is suited for applications with low-demand heat transfer requirements
- Double wall design: An outer shell houses an inner shell, creating a fluid flow passage between the two. A spiral baffle is used in the flow passage to produce an engineered flow channel to precisely control fluid velocity, direction, and turbulence
- Mono-flow (one direction) configuration: Fluid enters one end of the roller and exits through the other, keeping inlet and outlet rotary union sizes to a minimum. Mono-flow configuration is often used when higher flow rates are required
- Duo-flow (two-direction) configuration: A specially designed rotary union is used so fluid enters and exits out of the same roll end. The benefit is in keeping all machine piping on one side and freeing up the other end of the roll for drive connections. Drawbacks to a duo-flow configuration include restricted flow passages and the rotary union size must increase to handle the same flow rate
- Non-contact spiral with controlled flow-over design: Double wall, internally baffled roller that has a closely controlled gap between the spiral and the ID of the outer shell. This eliminated dead zones in fluid flow and hot/cold spots on the roll surface
- Full-contact, interference design: This "strength" construction double wall, internally baffled roller has a precisely machined spiral with a heat-shrunk outer shell to create an interference fit. The structural rigidity of the inner and outer shells provides higher load-carrying capacity. A welded spiral wrap or a spiral flow passage can be machined into the surface of the inner shell
- Manufactured to print or engineered specifically for the end-user’s application
- Designed and manufactured for value, performance, and to exceed industry standards
- Precision-machined to meet finish and geometric tolerances
- Engineered for guaranteed thermal and physical performance
- Designed and constructed for consistent temperature control across the roll face (+/-1°F)
Connect with
PRS Experts
Questions? Tough challenge? Need a second opinion? The PRS experts are here to guide you to your next-level engraved or precision roll solution. Set up a consultation today!