Gravure sets the standard for unparalleled precision, customization, and consistency in high-volume, high-quality printing applications.
After more than a decade of involvement in electromechanical engraving for gravure rolls, I’ve had the privilege of learning from some of the most seasoned experts in the field — my PRS colleagues with many decades of experience. This unique blend of seasoned wisdom and fresh perspective is keeping PRS at the forefront of gravure printing innovation.
Many of our team members have been perfecting their craft for decades, offering a depth of knowledge that's irreplaceable in any industry. Their experience, combined with our commitment to embracing new technologies and techniques, enables us to tackle the evolving challenges of modern printing with time-tested methods and cutting-edge solutions.
This article explores the current state and future directions of gravure printing, and how modern practitioners balance traditional techniques with technological advancements. From large-scale projects like flooring rolls to precision work on pharmaceuticals, we’ll examine how gravure printing continues to evolve and adapt to meet complex manufacturing challenges.
Gravure Printing: Precision Engineering in Action
Gravure is a technique used for high-volume, high-quality printing in industries ranging from pharmaceuticals to flooring and more. At the heart of gravure engraving are the millions of microscopic cells etched into the print cylinder’s surface.
These cells hold the ink or other substances that will be transferred to the substrate. The size, shape, and depth of these cells are tightly controlled to achieve the desired print quality and ink volume. The precision of these engravings directly affects print quality and roll longevity, making it a demanding process that requires meticulous attention to detail.
Gravure engraving allows for incredibly tight tolerances, down to +/- 2 microns for certain applications, while also achieving control over exacting geometries and dimensions. Key technical parameters include:
- Lines per inch (LPI): Measures the number of engraved lines in an inch
- Billion cubic microns per inch squared (BCM): Quantifies cell volume capacity
- Grams per square meter (GSM): Gauges the weight of ink laid on the substrate
These specifications are critical for achieving consistent and high-quality prints, especially over large production runs. At PRS, we pride ourselves on being a one-stop-shop for our gravure printing customers. Our end-to-end solutions mean that we handle everything from initial consultation to final product delivery. This comprehensive approach ensures that every step of the process is meticulously managed, resulting in superior quality and consistency.
Tackling Gravure’s Complexity & Managing Tolerances with Advanced Engraving Techniques
Electromechanical engraving is a core technique we use at PRS. It can have a profound impact on the quality of printing outcomes in several key ways:
Precision and detail: This is essential for producing high-quality prints with fine details, sharp images, and accurate design reproduction. The ability to engrave tiny cells with accuracy measured in microns ensures ink transfer is consistent and reliable, resulting in clear, vibrant results.
Consistency: By precisely controlling the depth, width, and shape of each cell on a roll, electromechanical engraving ensures that each print is identical to the last. Industries like packaging depend on uniformity in print quality to support brand recognition and consumer trust.
Control over ink transfer: Precise control over cell dimensions is key to controlling ink transfer. Expert engravers can fine-tune parameters such as LPI, BCM, and GSM to match specific requirements for ink density and distribution — which are essential for producing high-quality images and crisp text.
Ability to handle complex designs: Electromechanical engraving technologies enable the creation of complex and intricate patterns, textures, and gradients that are difficult to achieve with other engraving methods. This capability is beneficial for applications that require detailed artwork, such as high-end packaging, currency, and decorative printing.
Versatility in applications: Whether the substrate is paper, plastic, metal, or another material, advanced electromechanical engraving techniques are needed to craft the required cell patterns for high-quality printing. This versatility makes gravure printing a preferred choice for widely diverse industries.
Durability and longevity: Precision-engraved gravure roll cells, together with highly durable roll materials, ensure these rolls can withstand extensive use without degradation in print quality over the course of a single run — or over years of continuous use. This is particularly important for significant cost savings and reduced downtime in high-volume applications.
Customization and flexibility: Electromechanical engraving techniques allow for the creation of bespoke solutions tailored to specific customer needs, such as differentiating products through custom designs.
Waste reduction and efficiency improvements: Pinpoint accuracy in engraving minimizes the potential for printing errors and can help optimize for usage of materials like ink and adhesives, helping customers control costs, reduce waste, and minimize the use of solvent-based inks and other materials with negative environmental impacts. Efficient transfer and fewer reprints help make printing more sustainable.
Electromechanical Engraving for Gravure Printing: From Concept to Cylinder
At the heart of gravure engraving are microscopic cells etched into the cylinder's surface. These cells hold the ink or other substances that will be transferred to the substrate. The size, shape, and depth of these cells are meticulously controlled to achieve the desired print quality and ink volume.
Customization: Tailoring Solutions for Every Client
Understanding Client Needs
The process begins with a thorough understanding of the client's requirements. This includes:
- Assessing what they're currently using
- Identifying what's important to them (e.g., tolerances, specifications)
- Determining if they need artwork creation or modification
The Power of Precision
Gravure engraving allows for incredibly tight tolerances. For example:
- Tolerances as tight as ±2 microns for certain applications
- Ability to start engraving at exact measurements (e.g., 12.55 inches from the shaft)
- Precise control over engraving width (e.g., 47.613 inches wide)
This level of precision ensures consistency across massive production runs and can be critical for applications where accuracy directly impacts safety or functionality.
Industries Served: From Flooring to Pharmaceuticals
Gravure cylinders for flooring are among the largest in the industry, with face lengths over 200 inches and diameters exceeding 20 inches. These massive cylinders require specialized equipment and expertise — capabilities not all roll solutions providers can offer.
On the other side of the spectrum, the pharmaceutical industry relies on gravure engraving for pill marking and packaging. Even candy production demands precision-engraved gravure cylinders to achieve consistent, on-brand marking on every individual piece produced. A single cylinder might be responsible for producing millions of individual items.
The Engraving Process: From Concept to Cylinder
1. Artwork and Design
The process often begins with artwork creation or modification. An engraving partner with skilled designers on staff can:
- Clean up rough or low-resolution images
- Add seamless repeats to patterns
- Adjust colors and contrasts
- Create entirely new, bespoke patterns
2. Proofing and Approval
Before engraving begins, PRS provides customers with detailed proofs, including:
- High-resolution images of the proposed design
- Visualizations of how the design will repeat on the cylinder
This step ensures client satisfaction and serves as a final check before the engraving process begins.
3. Engraving Techniques
Our engraving experts select from various techniques depending on the application:
- Electromechanical engraving for precise cell creation
- Laser ablation and chemical etching can also be used to achieve highly customized cell shapes and depths
4. Quality Control
Throughout the process, rigorous quality control measures are implemented. Our teams consult and collaborate with customers to establish the optimal QC checks, and report back at major production milestones, including:
- Microscopic examination of cell dimensions
- Depth scans to ensure consistency
- Multiple measurements across the cylinder’s surface
Technological Advancements in Printing: The Value of Expertise & Craftsmanship
While gravure remains a preferred method for many applications, the industry continues to innovate. Our experts continually explore new materials for resist coatings, opportunities to improve process efficiencies, and techniques for crafting and quality inspections.
In an industry where microns make a difference, the value of experience is hard to overstate. In some cases, enduring customer relationships result in our experts having intimate knowledge of long-running equipment and machines’ quirks and capabilities, so they can anticipate, adapt, and trouble-shoot more effectively in the production process.
We see firsthand the value customers can get by choosing a partner who truly understands the complexities of engraving for gravure printing. Our experts are regularly called on to:
- Advise and inform customers on design and production choices
- Troubleshoot and address issues that can arise throughout production and use
- Offer insights that can improve the final product
The Future of Engraving for Gravure Printing Balances Tradition & Innovation
The future of engraving will be shaped by changing customer demands. As consumers and end users continue to expect high-quality, consistent outcomes and more sustainable practices, gravure engraving remains an important capability for printing. Its ability to provide unmatched precision at scale will support its relevance for years to come.
The key to success in this field lies in balancing traditional craftsmanship with cutting-edge technology, all while remaining adaptable to changing industry needs. As we look to the future, gravure engraving will continue to evolve to meet new challenges and push the boundaries of what’s possible in industrial printing.
Whether your next project begins with a legacy pattern in need of refinement or detailed repair to an existing gravure roll, reach out to the electro-engraving experts at PRS. Our team of seasoned professionals with decades of combined experience is ready to tackle even the most challenging projects. Contact a PRS expert today to discuss your specific needs and discover how our customized solutions can help you solve the tough challenges and achieve the results your customers expect.
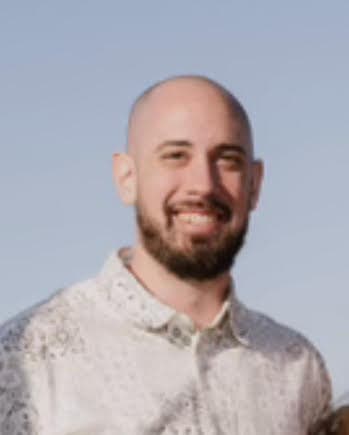
Written by David Muller
Technical Sales Representative
David brings a wealth of experience and a diverse skill set as a Sales Representative at Precision Roll Solutions. With eight years in the gravure industry, David has worked as a shift supervisor, engraver, polishmaster, grinder operator, electroplater, and programmer. His background also includes four years of service in the Marine Corps, showcasing his dedication and leadership.
In his current role, David engages directly with customers and sales prospects to provide engineering and design consulting, project management, and technical support. He works closely with customers who need help capturing, altering, or creating patterns to meet print and embossing design needs, with the help of the PRS design team. He also helps anilox roll customers precision-adjust patterns to optimize ink and coating application.
He appreciates that he gets to play a key role in creating new print and embossing patterns that people interact with daily, often without realizing it. His hands-on experience as an engraver and production supervisor lends him unique insights into customer challenges and process issues to deliver tailored solutions.
Share Article:
Subscribe to PRS Blog Digest
Share Article:
Connect with
PRS Experts
Questions? Tough challenge? Switching vendors? The PRS experts are here to guide you to your next-level web converting roll solution. Set up a consultation today!